В чертеже был обозначен пластик римамид, но партию опорных колес наша команда изготовила из капролона, который обработали на токарном станке. Почему выбрали другой полимер – рассказываем в статье.
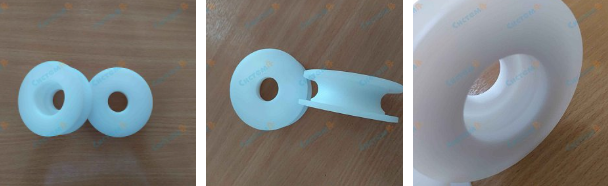
Вспоминаем интересный проект! Заказчик, крупная горно-металлургическая компания, поставил задачу изготовить партию деталей согласно конструкторской документации.
В чертеже был указан требующийся для производства деталей пластик – римамид. Этот модифицированный полимер часто становится основой металлозаменяющих комплектующих за счет улучшенных эксплуатационных свойств – он высокопрочный, долговечный, имеет низкий удельный вес, обладает отличными антифрикционными свойствами за счет низкого коэффициента трения, высокой стойкостью к износу, а также хорошо поддается обработке на токарных и фрезерных станках.
Мы предложили заменить его популярной маркой полиамида – капролоном. Такое предложение было озвучено нами после тщательного изучения технического задания. Наша команда пришла к выводу, что эксплуатационные качества полиамида-6 идеально подойдут для решения поставленной задачи – требовались опорные колеса, стойкие к износу и коррозии. Клиент изучил наше предложение, сопоставил эксплуатационные качества и цену обоих полимеров и согласился заменить римамид.
Партию из ста деталей изготовили на высокоточном токарном станке с числовым программным управлением.
Размер единицы – 100х34 мм. Клиент высоко оценил свойства и качество сырья, а также точность обработки. Ждем новые заказы!